製品の企画・開発・設計における取り組み
製品の企画・開発・設計の段階で、製品事故予防に向けた取り組み
弊社では製品の起案から、安全製品開発フローチャートに基づいた9つの安全確認を行っています。 開発段階では、製品コンセプトをまとめたコンセプトシート、製品に求められる機能や要望をまとめ、製品機能要求を盛り込んだPLPエビデンスシートを作成しています。
製品の設計・企画段階において、社内データベースや、製品評価技術基盤機構NITEのデータベ ースを活用し、さらに外部専門家※への委託などで、最新の製品事故情報(類似品含む)の確認を行っています。懸案事項があれば、PLP(事故予防策)エビデンスシートに記載し、対策案を講じる対処を行っています。
その後設計を進めていく上で、図面だけでは判断のできない問題を明らかにするため、実際の製品に近い試作品を製作し、試験を行っています。 また、図面が出来上がった段階の製品化決定DR(デザインレビュー)では営業部・品質管理課・購買課・開発設計課が集まりコンセプトシート・PLP(事故予防策)エビデンスシートに沿った設計がなされているかチェックし、製品の評価を行っています。
金型製作前には金型構造や製造時に起こりうる不具合の検証を行っています。 試作品の強度試験・耐久試験・組立実装など各種試験を行い、求められる品質が得られるまで設計変更を行っています。 また、製品の属性により各種試験や検証が適正に行われていた事を品質保証部が承認し、製造工程に着手しています。
※外部専門家とは以下です。
リスクアセッサー、製品安全デザイナー、プロダクトデザイナーなど。
仕入先の管理として「仕入先評価選定表」を用い、新規取引開始前に評価を行っています。 選定評価内容としては、経営基盤・生産能力・品質管理・価格の4分類16項目を評価し、総合評価にて適正性を確認しています。
製造時の製品の安全性確保のための取り組み
①仕入先選定は、製品のリスク評価後に求められる品質を備えた技術力、製造力を基準に決定しています。
②製造時に起こりうる不具合の有無を事前に把握し不具合があれば対策しています。
③初回量産時に製造工程に立ち合い、決められた手順で製造・検査が行われているか確認を行っています。
④部品検査規格に基づき、量産時の工程検査と入荷品の受入検査を行っています。
⑤原材料のMSDS等を入手し、材料の成分分析の把握を行っています。
⑥原材料は、X線蛍光分析器にて検査を行っています。
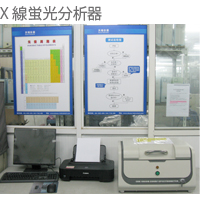
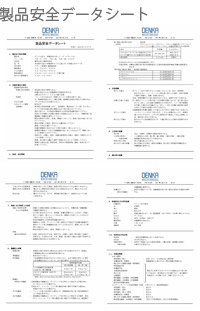